Spec. It’s a short-form word that many in the trucking industry are quite familiar with. While, by definition, it stands for specification, for purchasing managers and owner-operators, it stands for everything from profitability to business growth. Why? Because if you aren’t using the right equipment your entire business model could be at risk.
While you may be looking at vocational trucks, most large commercial motor vehicle purchases are those of traditional tractor trailers, so we will focus on those in today’s article. The fact is, on average, it costs a dollar per minute to keep a big rig in the shop. To avoid finding yourself on the high end of that average, it is critical you spec the right equipment before the rubber hits the road.
Smart operators manage to lower overall cost of equipment acquisition by doing the research required to ensure they purchase equipment with specifications that match their business needs. There is little benefit for a motor carrier or owner-operator to spec a Class 8 heavy-duty commercial motor vehicle if all they need to do is complete small package runs.
Still, this does not mean that a fleet should rely on spec’ing alone and ignore vehicle maintenance for years at a time. You want to successfully keep a truck running for at least 500,000 miles without any significant maintenance or parts replacement costs. Spec’ing the right truck (and trailer, which we will get into later) is important, but ongoing maintenance, whether preventative or not, is critical to maintaining a healthy fleet.
This shouldn’t be hard considering preventative maintenance intervals have lengthened from 10,000 to 15,000 miles to anywhere from 40,000 to 50,000 miles, depending on the application and engine specification. At the extreme ends, some engine models can extend out to 70,000 miles between oil change intervals. Preventative maintenance should never be extended to that length, but oil change intervals provide a little more leeway.
Spec’ing for the Long Term
When you are making critical equipment purchase decisions, you must be thinking not only about the type of work your equipment will be facing, but also what the long-term view is. It is important to look at equipment ownership and maintenance concerns from both the short and long view; both the small and big pictures.
Short-term considerations include regularly inspecting fluid levels, checking for progressive wear on specific pieces of equipment, and ensuring DOT stickers are readily visible. Long-term business considerations involve things like spec’ing equipment, preparing for regulatory change, and figuring out life-cycle costs.
Consider disc brakes as an example. While disc breaks may sound like a short-term consideration, they actually represent the long-view. Although the full life-cycle costs of discs compared to drum brakes is about the same, the reasons why are different. While drum brakes might cost less at the outset, they generally require more maintenance over the long-term.
Disc brakes are far more reliable and work using fewer parts, yet they also require regular inspections. Avoiding pad changes on air disc brakes right around mid-life is not a good idea. If you wait too long, you may irreparably damage your rotors, which could be up to a $3,000 mistake.
The Best Spec Guidance
The best guidance is to spec to your commercial motor vehicle’s most expensive time frame, which are generally years three or four. If you purchase equipment based on when it will cost you the most and then plan for that, you will be in a far better position to save your bottom line while also encouraging good purchasing decisions.
Another example of spec wisdom lies in alternators. While purchasing a high-efficiency, high-output alternator, you might find the upcharge a bit hard to swallow. Yet, it is critically important that you understand, the up-front cost increases are vastly eclipsed by your long-term savings in fuel savings, efficiency, fewer battery problems, less no-starts and so much more.
Depending on the application, a high-efficiency alternator can save a truck driver or fleet up to $100 a year on fuel costs alone. If the alternator is keeping the battery charged for longer, then you may not need to replace them as soon as usual. When you factor in all these intangibles, the more expensive alternator suddenly seems like a pretty good decision.
If you are engaging in vertical integration of your spec’ing choices, then you will be better prepared to absorb premium item costs by reducing costs elsewhere. Where technology giveth’, technology can also taketh’ away. Just remember that even though you must pay a premium for some of the advanced items and technology you need to set you up for the future, upgrades to existing equipment is rarely money wasted.
Looking at the Parts Problem
Motor carriers – and business in general – like to stick to what they know. For this reason, they can sometimes overlook part changes or efficiency upgrades. Fleets should always put their faith in the hands of the OEM(s) where spec’ing certain parts is concerned. If you are making these changes for your business, then make sure you are doing it based on real data and experience.
It never hurts to inquire with your partners regarding their experience is in handling a specific build or parts-related problem. Even more, managers want to ensure they are paying close attention to the availability of parts. If you have a tractor spec’ed out with all the bells and whistles, make sure you have a backstock of parts in the wings so that when something breaks, you’ve minimized downtime by being prepared.
A good rule of thumb is to swap the general theory that standard parts should be well-stocked and rarer parts not. If your application demands it, you may be spending far more time on replacing rarer parts. Keeping tier inventory levels at equilibrium is a great option. Why? Because heavy-duty commercial motor vehicles are built pretty well these days.
Decades ago the industry worried (rightfully so) about things like drivelines, transmissions and axles, but the build quality has improved dramatically with new manufacturing and fabrication techniques coming online. Today, shop managers are more concerned with aftertreatment systems than they are with engines. Telematics, electronics, and sensor technology all require extra attention.
Bye-Bye General-Purpose Truck
Another dying holdover from a decade ago is the “general-purpose” truck. Today, because of the varied nature of freight transport, truck specs must be duty-cycle dependent. You would be doing your business a disservice by running an OTR vehicle in a P&D operation.
This makes getting the specs right from the very beginning absolutely critical. The last thing you want to do is be faced with having to fix something after the fact because it was not initially spec’d properly.
The most important thing is to consider the cost/benefit analysis of spec’ing premium components if it means long-life and a largely maintenance free existence. And finally, consider the application when deciding on a vehicle. How you run the truck plays a large part in its future maintenance and upkeep profile.
What About the Trailer?
While the truck is important, without the trailer to haul the goods in, there would be no reason for the tractor to exist. Yet, trailers wear out just the same as the trucks that pull them. General trailer wear-out generally lands somewhere between 10 and 15 years. Those operating in the truckload sector generally see the shortest trade cycles, while grocery companies tend to keep trailers for 12 years or more.
Motor carriers operating in the food service space generally keep their trailers for longer periods of time because they are built to last in low-mileage, high-cycle situations. In the truckload sector, however, trailers tend to run less miles, quite simply because of the higher tractor-to-trailer ratio.
Some of the most common problems with trailers are electrical, which is why spec’ing a high-quality wiring harness is so important. If the trailer experiences any jarring or sudden movement, cheap electrical setups frustrate truck drivers, especially when failures occur on the road.
The biggest killer for electrical components in trailers – outside of poor harness jobs – is moisture. No matter what you are spec’ing, whether on tractor or trailer, it is vitally important you take great care to ensure seals, gaskets, rivets, and more, are all firmly in place, dry, and ready to repel water.
It’s All About Maintenance
In the end, it won’t matter what you spec if you don’t have a comprehensive preventative maintenance program in place to ensure your equipment stays in good shape over the long haul. If you are running a spotty maintenance program, or are not enforcing preventative maintenance measures, all your spec dreams could go right out the window.
Why invest in tire inflation systems or air disc brakes if you are not committing the manpower and resources required to ensure they stay properly maintained? While equipment like this might get you through longer periods without routine maintenance, but it doesn’t eliminate the need for it altogether.
Invest in your shop, keep your fleet technicians happy, and pay close attention to properly spec’ing at initial purchase, and you will be sure to enjoy a long, fruitful life with your essential equipment.
from Quick Transport Solutions Trucking Blog https://ift.tt/2u9Jbrx


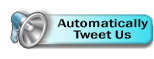
Sourced by Quik DMV - CADMV fleet registration services. Renew your registration online in only 10 minutes. No DMV visits, no lines, no phone mazes, and no appointments needed. Visit Quik, Click, Pay & Print your registration from home or any local print shop.
No comments:
Post a Comment