
By Christopher Lyon, Director of Fleet Relations, NTEA – The Association for the Work Truck Industry
Fleet professionals are tasked with providing safe, reliable and compliant vehicles for their organization. In many cases, fleet professionals that design these work trucks only have indirect control and/or input on how these vehicles are used after being placed in service.
One of the biggest concerns is understanding the consequences of operating overloaded vehicles. This includes drivability issues, reliability and maintenance concerns, and the regulatory impacts and liability risks associated with operating overloaded vehicles. With some forethought in the vehicle design phase and broad-based education for all stakeholders, these issues can be minimized, if not completely eliminated.
What is an overloaded vehicle
Industry professionals generally know gross vehicle weight rating (GVWR) represents maximum vehicle weight, including chassis, body, auxiliary equipment and payload. Several other factors beyond GVWR can contribute to a truck being characterized as overloaded, including gross combined weight rating (GCWR) and gross axle weight rating (GAWR). GCWR is the maximum allowable weight for a truck and trailer combination. This covers the weight of the truck, any cargo and the trailer. In short, if the load rolls with the truck, the weight is included in GCWR. GAWR covers each axle on a truck and trailer. It is limited to the weakest component in the axle system, including suspension, tires and brakes.
Drivability — Controlling a vehicle
Improperly loaded vehicles or those that exceed the weight rating will have a dramatic effect on performance. Steering, maneuverability, braking and acceleration are all affected. Most important, stopping distances are dramatically impacted. Simply stated, an overloaded truck requires more distance to stop. Operators can misjudge necessary stopping distance when a vehicle is improperly loaded.
Another example is maneuverability and steering (i.e., when a vehicle exceeds weight on the rear axle which creates an imbalanced load). These factors can affect the entire characteristic of the truck. Steering and handling are impacted, and in extreme cases, the truck loses front axle traction.
Excess speed and maneuverability are significant issues (i.e., a large vehicle traveling down an incline can gain additional speed paired with decreased maneuverability and stopping distances). All these scenarios can cause immediate and unsafe conditions for the vehicle, operator and general public. Isaac Newton’s laws of physics state items in motion stay in motion, and objects at rest will stay at rest until compelled to change action by an external force. Manufacturers recognize these effects in vehicle design and the influence external forces have on important components like brakes, powerplants and powertrains. All these critical components are set to operate within a specific range of parameters. Ultimately, these design characteristics recognize the physics within the operating environment.
Maintenance — Keeping trucks on the road
Downtime can be a major expense for any organization. Idle equipment is not producing work. Components broken as a result of exceeding capacity can be completely preventable. Another significant educational opportunity is the cost of downtime. At times, vehicles are overloaded with the misconception of being more efficient. Operators believe streamlining to one trip can save time and money. However, a preventable breakdown affects drivers and customer commitments and can even require a larger fleet due to the need to retain maintenance spares — all of which are unnecessary expenses.
Overloaded and overweight trucks increase the cost of maintenance. Premature and preventable wear will drive up the cost of keeping trucks rolling down the road. Every operating system will be strained. Failure rates on many components will increase due to added stress. Tie rods, steering arms, tires, engines and other drivetrain components will wear prematurely as a result of operating above design tolerances.
Avoid risk and liability
Some drivers and supervisors in the fleet industry may think they are exempt from mandated weight restrictions/limits. There may be some organizations that have an exemption or may be permitted to run an overweight vehicle on the road. However, no one is exempt from having safe and compliant vehicles. This means vehicles cannot exceed designed weight capacity, under normal operating circumstances.
Consequences are costly. Though state laws vary, overweight tickets are often expensive and can lead to impounded vehicles. Many vocational trucks do not have a working familiarity with regulatory compliance as their vehicles are not routinely crossing mandated weight stations (often seen on highways).
Fleet professionals may not have as much control once the vehicle is on the road, but education can be an effective tool. Training operators and upper management can often prompt improved policies.
As vehicle weight increases, so does the number of crash instances. In 2016, Federal Motor Carrier Safety Administration (FMCSA) data on large trucks and buses show crashes are directly proportional to vehicle weight. This data suggests that adding weight only increases the chance of an occurrence. Furthermore, as a fleet professional, a duty of care is held for the operator and organization. In the event of an incident, there can be civil and criminal consequences; respondeat superior — Latin for “let the master answer” — infers a responsibility that can go beyond the operator and include the fleet design team as well as others within an organization. If it is determined the vehicle was overweight, there can be severe civil and criminal penalties. Although it varies by state, in the event of a fatality, there are statutes that can hold an operator or owner criminally responsible, including charges as severe as manslaughter.
Controlling weight
There are several ways to prevent overload. First, it is important to understand how trucks are actually used. Many times, there is a disconnect between the design team and end users. Making field observations, talking with end users can be much more productive than assuming user awareness and willingness to abide by vehicle design parameters. Often, telling end users how to use equipment will fall on deaf ears. In the end, they have a job to get done and will find a way to use equipment, whether it was designed for the task or not.
Underutilized space
Unfortunately, on work trucks, you will rarely find underutilized space. Eventually, end users will add items to fill the void, resulting in unnecessary weight if the added materials/tools are rarely used. Too much space can add weight as operators may find items to fill room that’s not mission-critical. When adding weight, end users contribute to physical capacity, without taking vehicle effects into account.
Available tools
When designing a work truck, there are several tools you can use to provide a safe, reliable, compliant work truck. Accounting for reserve weight and not constantly running at maximum capacity help reduce maintenance and operating costs. In addition, considering reserve weight allows a cushion to add more, if needed. When planning for payload reserve ability, it’s typically appropriate to operate a vehicle between 80 percent and 85 percent capacity, leaving 15 percent to 20 percent reserve capacity.
When designing, consider engaging NTEA’s Vehicle Center of Gravity and Axle Weight Calculator — a web-based, interactive tool that provides vehicle specification and weight information. When upfitting or modifying a vehicle, these calculations produce information to share with customers, and assist in understanding how certain industry standards may apply — both in spec’ing prior to purchase and after upfitting is complete. Interactive instructions make this a user-friendly, additional tool for those in your company who are responsible for weight distribution and center of gravity calculations. The calculator is a free member benefit — not available for public purchase (details at ntea.com/weightcalculator). This data provides a helpful framework for reserve payload.
Striving for optimization
The goal is designing a work truck that encases all elements of performance, fuel economy, maintenance, resale and versatility. Sitting down with stakeholders to create and prioritize a selector list often exposes compromises. It’s critical to understand these concessions and how they affect drivers and equipment supervisors; meet expectations from internal and external customers; and influence the bottom line.
Completing a life cycle cost analysis can help you make concrete financial decisions. NTEA’s Vehicle Life Cycle Cost Tool performs calculations on scenario-based inputs, creating a pathway to determine true costs of ownership. It’s designed to be flexible and user-friendly to accommodate a variety of truck life cycle analysis needs and different fleet structures. This cloud-based resource enables fleets, engineers and sales representatives to load differing depreciation methodologies (such as straight-line, accelerated and pool depreciation techniques), fuel types, and regional fuel prices to fit the necessary truck or fleet analysis. Users can also incorporate the impact of income taxes into business decisions, where appropriate, and perform what-if scenarios. Depending on needs, the template can support single-vehicle comparison decisions, vehicle class analysis and whole fleet calculations. It can also act as a forecast tool when paired with a price sensitivity analysis — often necessary when dealing with volatile fuel price scenarios. The tool is a free member benefit — not available for public purchase (details at ntea.com/lifecycle). With this information, you are able to make strategic decisions and find the right vehicle for your organization.
Bottom line
Providing compliant vehicles is essential to your company’s success. Improperly loaded vehicles negatively affect drivability and reliability, and open your organization to unnecessary risk and liability exposure. These scenarios all have cost implications that can be avoided through education and proper vehicle design.
Learn more
NTEA offers fleet managers access to publications and reference materials on current regulations, safety standards, and other technical issues. To learn more about the tools, resources and solutions available exclusively to members, visit ntea.com/memberbenefits.
Established in 1964, NTEA – The Association for the Work Truck Industry represents more than 2,050 companies that manufacture, distribute, install, sell and repair commercial trucks, truck bodies, truck equipment, trailers and accessories. Buyers of work trucks and the major commercial truck chassis manufacturers also belong to the Association. NTEA provides in-depth technical information, education, and member programs and services, and produces The Work Truck Show®. The Association maintains its administrative headquarters in suburban Detroit and government relations offices in Washington, DC, and Ottawa, Ontario.
The post Understanding the Consequences of Driving Overloaded Vehicles appeared first on Fleet Management Weekly.
from Fleet Management Weekly https://ift.tt/2OEdrEX


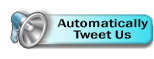
Sourced by Quik DMV - CADMV fleet registration services. Renew your registration online in only 10 minutes. No DMV visits, no lines, no phone mazes, and no appointments needed. Visit Quik, Click, Pay & Print your registration from home or any local print shop.
0 comments:
Post a Comment