Is your company caught in a “fail to scale” scenario? Bulk distributors that have grown through brute force must adopt technology to realize the potential capacity of existing assets. Automation strategies create new opportunities to reduce the number of delivery vehicles, total mileage and increase gallons delivered when adding another truck no longer does the trick.
Key metrics that indicate success are hard to evaluate if you don’t have a system geared toward optimization and insight. Keep reading to understand how technology investments are not just another expense.
The addition of new trucks can represent more delivery capacity, but if you have some untapped delivery capacity in your existing fleet, would it make sense to avoid buying more trucks by investing in automation technology? Similarly, new order entry clerks can add additional back-office capacity, but if you are just re-keying and duplicating work, would it make sense to automate your delivery workflows and integrate directly to your back office?
We’ve highlighted ways companies use technology to measure and manage their operations. In response to the idea that “You can’t manage what you can’t measure”, we’ve developed a maturity model for logistics maturity and what you need to get to the next level.
As companies invest in technology, they move from left to the right, from paper-based manual dispatching to fully-integrated companies that optimize routing, forecasting, and inventory.
Level 1 – Paper
Level 1 companies have paper-based dispatch with little or no software automation. Historically, everyone had to use paper. Most companies do not have sufficient systems in place to measure logistics efficiencies such as gal/hour or gal/trip since everything is paper-based. Level 1 does not necessarily mean you are highly inefficient or have poor customer service, but it does mean there are no processes and systems in place to deliver consistently and efficiently.
Level 1 typically views success as “Let’s make sure we make all of our deliveries…do not worry about overtime or whether we have too many trucks, just make sure everything is delivered.”
Many companies are reluctant to take the first step beyond Level 1 to begin implementing systems for dispatch because of a perceived risk to customer service and an inability to see beyond the expense. If you don’t have systems to capture and analyze data, you can’t grow your business and operate efficiently or predictably as your larger competitors do.
Level 2 – Basic Automation
At Level 2, logistics functions eliminate paper and allow information to be shared, and laying the foundation to measure efficiency. Since drivers use a mobile device, you know how long each trip takes so you can get bulk metrics reports like gal/hour, gal/trip and gal/mile.
The smartphone delivery app turns your truck into a virtual cash register that enforces a consistent set of delivery rules. Each barcoded tank lets you know the delivered quantity over time as well as that tank’s capacity and GPS location. It maintains product integrity by alerting/preventing the driver from delivering the wrong product to that tank.
Level 3 – Integration
Level 3 companies focus on moving from reaction-based logistics to resource planning. They optimize routes to determine how long a trip should take and measure performance with “plan-vs-actual” reports.
Example: The driver took 10 hours and drove 350 miles but should have taken 8 hours and 275 miles. At $25/hr and $2/mile, your plan saved $50+ in overtime and $150 in loaded mileage. You can see if the route ran out of sequence so you can take corrective action. Integration with your ERP means you are not re-keying orders, so the Order-To-Cash (OTC) cycle is shorter, and customer service is improved.
Level 4 – Visibility
Level 4 companies focus on using data to make decisions and have moved from simple route planning to optimize operations. Centralized dispatch is possible, which standardizes processes to ensure efficient and standardized delivery across ALL depots.
Many companies think site-based dispatch is more agile because their dispatchers “know the customers and territory,” but what happens when your dispatcher is sick or leaves the company?
The reality is decentralized dispatching reinforces inefficiencies. Level 4 companies use data to make better business decisions and have processes in place to ensure they can scale. They don’t have to worry a single dispatcher will make or break their operations and quality of service.
Level 5 – Optimization
Industry-leading companies with Level 5 integration use automation to achieve higher profitability, higher customer satisfaction, and lower waste. Now that all of your tanks are barcoded, you forecast orders for unmonitored tanks using Machine Learning. Instead of topping off keep-full accounts, you schedule deliveries based on when the tank needs to be filled, resulting in larger drop sizes and increasing your average gal/delivery. Instead of delivering 1x/week, you deliver 2x every three weeks and use the extra capacity on the truck to service more customers.
Level 5 includes multi-vehicle, multi-compartment optimization. The software routing engine optimizes orders across vehicles to ensures optimization for the lowest total transportation cost while still meeting customer service windows.
Example: The routing engine will take ten trucks with 100 orders and assign orders to trips, so the net result is meeting all customer service windows but only using 8.5 trucks. Optimization gives you extra capacity that equals an extra truck and driver.
Multi-vehicle, multi-compartment route optimization tends to be used in companies with more than 50 trucks. There are a few companies that advertise multi-compartment routing, but in our real-world experience, there are only a couple that achieves it. Dynamic, multi-compartment routing requires a high level of sophistication and commitment. Multi-vehicle, multi-compartment routing has proven to save an additional 10-25% of your total transportation costs depending on the density of your delivery area and the number of stops per day per truck.
“What gets measured gets managed” is our first article in a series to help companies understand their logistics maturity and find tools to measure and grow their business. Future articles will cover the steps needed to move from Level 1 to Level 5. We will share why companies decide to invest in technology and the benefits your company can expect as it moves through the maturity model. If you have questions or would like to learn more, please contact us.
from Apps for last mile logistics | routing and dispatch https://ift.tt/2HAbUNU


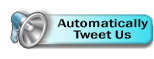
Sourced by Quik DMV - CADMV fleet registration services. Renew your registration online in only 10 minutes. No DMV visits, no lines, no phone mazes, and no appointments needed. Visit Quik, Click, Pay & Print your registration from home or any local print shop.
0 comments:
Post a Comment