
Data Driven Logistics
Multi-compartment route optimization can save 20% of your total transportation costs by creating smarter routes and using more of your trucks’ capacity.
If you deliver bulk products and have more than 10 trucks/depot and don’t use multi-vehicle/multi-compartment routing, you’re missing opportunities to improve operational efficiency and customer service.
Multi-compartment routing allows you to define capabilities and a compatibility matrix so the optimization software can build the lowest cost routes, use the least amount of trucks and still meet customer delivery constraints like service hours.
There’s a lot wrapped up in this statement, so let’s outline what the optimization process does and how you use a multi-compartment routing solution. Our solution differentiates itself in multi-compartment routing, especially with products like lubricants where combo trucks have a variable number of compartments. There are 3 keys to our multi-compartment routing solution:
- Compatibility matrix
- Capabilities and calendars (service windows)
- Route optimization
Step 1 – Compatibility Matrix
The first step of the configuration is setting up trucks and trailers with compartments and compatibilities. For example, a tank-wagon may have 4 fixed compartments plus 2 slots for pallets. Or a combo truck may have 10 slots that are all variable, where slot 1 can contain a pallet today and a bulk tote tomorrow.
For each compartment, you define the allowed products (compatibility matrix), filling requirements, volume and total weight. These will be factored in to prevent over-filling as well as being over-weight.
Our solution has service capabilities per compartment, along with filling requirements. An empty clear diesel compartment can take dyed diesel, or a 0W20 can take a different lubricant if the compartment is washed. This applies to all bulk products, so you can have the same filling compatibility whether you are filling organic milk on top of regular milk, 0W20 on top of 5W20, or 8% bleach on top of a 12% bleach.
The optimizer understands variable compartment layouts where slot 1 contains a 500 gal tote today but tomorrow contains a 330 gal tote. The compatibility matrix is a key part of the setup.
Step 2 – Capabilities and Calendars
In the optimizer, you can define capabilities on any resource, including trucks, trailers, drivers, customers, etc. A capability is a user defined feature such as “metered vehicle” or “high speed pump”, so you can match truck capabilities with customer or product capabilities. For example, you can state that bulk lubricants require the capability “meter”, so only metered vehicles with valid compartments are considered for bulk lubes orders. Or you can state customer 123 only has the capability for “short trucks” so you don’t route full trailers that may not fit.
A capability can also be assigned to a driver, such as “mine safety certification”, so only drivers with that capability will be routed on orders that have customers meeting the same capability.
Capabilities are most often assigned to trucks/trailers. If you have a specific piece of equipment it will only be matched to orders that have that same capability.
In addition to capabilities, you can assign calendars to resources, just like you assign capabilities. The most common resource calendar is customer service hours. You can establish multiple service hours per day so the routing engine will determine if you can meet that calendar, such as only deliver between 8am-10am and 1pm-4pm so you don’t block dock bays during peak windows.
Additionally, you can add one-time calendars such as Thanksgiving or Christmas where customers are closed or have limited service times.
The optimizer considers both capabilities and calendars, with the option to highlight when a route can still be considered but may have a “soft constraint”. This comes into play when a customer may close at 5pm but the optimizer shows you would complete the order at 5.10pm, or when orders on a truck total 1010 gals and the compartment holds 1000. The dispatcher can still accept the route after acknowledging the violation of this constraint.
Step 3 – Route Optimization
Optimization is the process of automatically building routes (trips). The optimizer assigns resources (drivers, trucks, trailers) and stops (orders, loads) to create the lowest total transportation cost to service all orders. The optimizer considers compatibility matrices, capacities, constraints and calendars to ensure the most efficient routes are built and comply with your business rules.
The simplest example is a depot that has 10 trucks and 100 orders. The optimizer will automatically build routes and may determine you only need 8.5 trucks.
Many customers worry that “all the knowledge is in my dispatcher’s head” and you can’t automate that – my dispatchers know the geography and the customers.
Dispatchers’ territory and customer knowledge is important, but how do you know they’ve done a good job? How do you know how many miles they should drive, how long it should take and that you’ve used your assets most efficiently? Without a planning tool, you don’t know. And without a mobile solution, you don’t know driver actuals or route compliance. Without delivery metrics, you miss key data to measure logistics efficiency.
Moving from paper and older dispatch systems to a multi-vehicle, multi-compartment optimization allows you to centralize dispatch and establish a foundation for “Data Driven Logistics”. Route optimization allows you to take the knowledge from your dispatchers’ heads and formalize it in software to get efficiencies of scale and provide tools to make dispatchers more efficient.
The optimizer provides the plan while the goRoam mobile app provides the actuals and up to the minute delivery status. goRoam enforces route compliance and can be configured to require a 1-time PIN code from the dispatcher for the driver to go out of sequence. goRoam is specifically built for bulk and package workflows, and includes capabilities such as barcode scanning of tanks, bulk inventory tracking, signature capture, mobile printing and compartment validation.
Our multi-compartment, multi-vehicle routing solution, along with the goRoam mobile app, provides the most advanced optimization and mobile solution specifically built for bulk logistics. Together we provide the platform for your “Data Driven Logistics”.
If you want a detailed analysis of how multi-compartment routing applies to your logistics, just click here…
from Apps for last mile logistics | routing and dispatch https://ift.tt/2mFw6pY


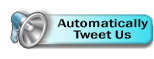
Sourced by Quik DMV - CADMV fleet registration services. Renew your registration online in only 10 minutes. No DMV visits, no lines, no phone mazes, and no appointments needed. Visit Quik, Click, Pay & Print your registration from home or any local print shop.
No comments:
Post a Comment