When it comes to the trucking and transportation sectors, the two big players in the game are motor carriers and shippers. Yet, there has been some friction between fleets and shippers as of late, as fleets contend their shipping partners are to blame for increasing detention times. Yet, with proper communication and visibility, these relationships need not be fraught! In fact, giving customers real-time visibility into the status of their freight has become the number one most desired attribute of a new trucker/shipper relationship.
Information is key to making the right decision in just about any situation. Whether a business operates in a brick-and-mortar environment or runs an e-commerce business, information is vital to decrease the chances for mistakes and increase overall efficiency. Many companies now demand visibility when it comes to their shipment. This is the only way to meet obligations to their customers without unnecessary delays.
On-Time All the Time
Many organizations are reliant on repeat customers. Missed deliveries or delays in receiving a shipment puts them at risk for losing those repeat customers. Many assume a problem with missed deliveries is only bad for e-commerce. In fact, brick-and-mortar stores also suffer. Many businesses rely on materials arriving at the right time so that they can assemble components.
Grocery stores and other businesses that deal with food also rely on on-time shipments. If there is a truckload of product coming and the end-receiver does not know it is going to be late, that could trigger a whole host of problems. The more inventory you have in your supply chain, the more susceptible you are to delays. As a result, shippers want to have as much information as they can.
Another consideration is in how precisely on-time a delivery is. And we aren’t talking about it only being late, but also being early. Today’s precision delivery standards require that truckloads are on time and full. If a truck arrives early, it could create complications for those on the receiving end. In fact, some have raised eyebrows in their approach. Walmart is just one example, such as when they announced they would begin fining suppliers for late deliveries.
Walmart believes in having the right product at the right place and right time for their customers. And they don’t differentiate what channel that product is going through, whether it is at the store or through their e-commerce channel. When a customer goes to a store or orders online, will the product be there? And if it is online, can they be assured they will receive the product?
Walmart used to have a very bulky supply chain. They have largely streamlined that, however, thanks to their growing e-commerce operation. Yet, it isn’t just the shipper or the receiver that is part of this conversation, but the trucking company as well. After all, the products or materials must get there somehow. And what is the main sticking point for those parties? Detention time.
Sent to Detention
Delays experienced by truck drivers at customer facilities have been on the rise over the past few years. It costs everyone in both time and productivity. In fact, the ATRI recently did a survey of 1,900 truck drivers between 2014 and 2018 to determine whether truck driver detention has been on the rise. Many of the survey responses said the problem is on the rise.
The survey also found that delay shave a knock-on effect down the entire supply chain. Subsequent pickups and deliveries were also found to be late as result of the original infraction. How much are these delays a result of unforeseen problems and because of fleet inefficiencies? The fact is, a lot of this can be traced back to facilities not increasing their labor or dock capacity to match increased freight movement and yard activity.
Many trucking companies experience dock staff that may not know exactly when the schedule is or know how to work the equipment. In some cases, there is a problem of serious understaffing. Delays can also be a result of shippers and receivers overbooking appointments or booked more trucks than they had the space to handle. Or there may not be the required equipment to unload them, even if they have the manpower.
The survey found that detention reasons remained consistent throughout the years from 2014 to 2018. The question is, when will interested parties make the necessary investments to improve detention time, whether it be through personnel or equipment changes or upgrades? It isn’t hard to figure out what needs to be done.
Potential solutions include a well-organized workforce, technology, and maintained and adhered to schedules and appointments. Even extending business hours as needed can have a big impact on overall delay times. When facility delays are one of the main problems impacting on-time deliveries, big investments may be required.
Interestingly, the survey found that women were more likely to be delayed than men, but this can be attributed to the fact that women are more likely to drive refrigerated loads. And since those kinds of loads are most often detained, that could account for the disparity.
In the end, as a result of the delays, fleets have begun charging shippers and receivers detention fees for excessive delays. These fees can range anywhere from $10 to $100 per hour depending on what is paid out to the truck drivers. The average comes in around $63. Still, the problem is getting the shipper or receiver to actually pay the fee. It can sometimes come down to a he said/she said game of who is at fault when a delay occurs.
From the Other Side
Fleets are always expected to make the delivery on time. Their business largely depends on it. Yet, whether someone gets somewhere else on time is not always up to the shipper. Welcome to detention time. When truck drivers are forced to sit and wait to be loaded or unloaded at a facility, that causes a lot of knock-on problems. Did you know that for the first time ever, truck driver detention made the ATA’s top trucking issues list for the first time in 2019.
Detention ties up a trucking company’s resources. But problems arise when a trucking company tries to bill the shipper for detention. All the fleet wants to do is free up their resources so that they can get out there and deliver more shipments. Even Walmart, who has its own private fleet, acknowledges that detention time can be a major headache.
Supply chain companies must maximize the time and availability of their resources. Companies are always looking for ways to minimize paperwork, red tape, and other obstacles to getting the job done quickly and efficiently. As such, they have begun using internal tools to aggregate information from motor carriers. Now, they are trying to determine if suppliers or trucking companies are causing delay issues.
One of the main complaints receivers have is that they may not get notified if a truck driver is not going to be on time. Even if it is not the trucker’s fault, say there was a road hazard or bad weather, simply receiving a notification of that allows them to readjust their plans for the day and reallocate their resources until the vehicle arrives.
It is important to note that detention time is not just a motor carrier or receiver or supplier issue. This is an issue that impacts everyone in the industry. All interested parties must work together to ensure the problem is addressed. Partners must work with each other, whether shipper, trucker, or otherwise.
When shippers evaluate carriers, of course they look at on-time service and safety, but what they really want is a partner who effectively communicates and doesn’t hesitate to provide up-to-date info, whether positive or negative. Truly good business relationships go beyond something merely transactional. They become true partnerships. But to get there, both parties must be effective communicators. The same holds true for just about any human relationship.
In the end shippers, receivers and trucking companies must all work together to ensure deliveries are made on time, no matter who it is coming from, going through or going to. The resiliency and reliability of our nation’s supply chain impacts everyone. Better partnerships can be built through improved communication and honest partnerships. Only this way can the entire industry raise its overall level of efficiency and see everyone prosper!
from Quick Transport Solutions Trucking Blog https://ift.tt/2VIPySa


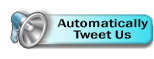
Sourced by Quik DMV - CADMV fleet registration services. Renew your registration online in only 10 minutes. No DMV visits, no lines, no phone mazes, and no appointments needed. Visit Quik, Click, Pay & Print your registration from home or any local print shop.
No comments:
Post a Comment