When it comes to the work a fleet technician does, tools exist to make the job much easier. The same holds true for truck driver training. But too many fleets are still clinging to old ways of doing things. Why not embrace a technological means of gaining greater efficiency and effectiveness in maintenance and training?
When it comes to heavy-duty truck repair shops, efficiency is the topmost priority. The goal is always to immediately identify the problem and fix it, 100% correctly with as much efficiency as possible. This is how you keep customers happy and get more business rolling in for the fleet. That’s why we wanted to take a moment to talk about how technological solutions help you increase productivity and save time and money.
A Closer Look at Shop Software
Whether you are the fleet technician, the shop manager or the owner of the company, you have a lot invested in maintenance. Your entire business model rests on a functional fleet. Most of all, the people at the front line of maintaining your fleet should be at top of mind.
So, how would you integrate a software-as-a-service (SaaS) solution into your maintenance profile? There are specific things to look for when you scout for a software solution, no matter what its use in your fleet might be.
- Does the software allow you to search by vehicle plate number or VIN?
- Can a technician search by fault code, symptom or component?
- Does the system provide a user-friendly layout for the technician using it?
Independent shop owners and large fleet shops alike want to look for very specific causes and components. Whether it be categorization by specification, testing procedure, wiring diagram or otherwise, if you invest in a shop software solution, it should be able to easily answer these questions.
Shops routinely rotate through a vast array of truck makes, models, and ages. Being able to sort through a database by make, model, or year saves the technician a lot of time. What did you do before? Navigate a dozen different OEM websites? If you do your homework selecting a software provider, you won’t have to worry about such things.
Make sure you choose a provider that offers an interactive and easily used web interface. You want intuitive and easy-to-follow instructions. The database should allow technicians to quickly and easily access information, so that they can then get on to doing what they do best, which is fixing heavy-duty commercial motor vehicles.
Speaking of fixing trucks, the last thing you ever want is a misdiagnosis. Not only does this present a critical safety issue but you may be saddled with big repairs simply because it was misdiagnosed to begin with. If you have a shipment out on the road, a broken-down truck could easily lead to a very unhappy customer.
Digging Deeper into the System
The scenario outlined above is exactly what a shop software should help you avoid. The key is to eliminate guesswork in a repair procedure. Consider how much modern trucks incorporate complex wiring and computing technology. If you have sensors, video, a sophisticated ELD, and in-cab entertainment – this is a very tough environment.
Effective software solutions should offer colored, scalable wiring diagrams and layouts. Many fleet and independent shops have been on a technician hiring tear. The battle for skilled workers is not relegated to the cab only. As the US economy has improved, job openings are a-plenty. Do you want lower-skilled workers at the helm of a complicated repair without an effective job aid?
Many new technicians may be fresh out of trade school and have little experience in complex repairs on modern vehicles. While you do want to run an effective coaching and training program – which we will get into later – an online or on-site digital job aid might be just what your new technicians need. Rather than wading through technical data online, the appropriate information can be built on an intuitive digital system.
Technicians should have quick, reliable access to graphical step-by-step walkthroughs of any repair procedures that may come up. An indiscriminate online search carries a high level of risk and paranoia that the job may go wrong.
Another aspect of the system should be how well it integrates into other systems. Interoperability is very important if you are utilizing multiple pieces of software or an overarching fleet management system. How easily can you download and upload information? Can you view a variety of business reports or repair orders filtered however you want to filter them?
Fleet and shop managers who want to see how the shop is doing should be able to easily access performance metrics based on vehicle up-time, inventory, and efficiency. They should also be able to access repair information for various makes and models of trucks the shop services.
Advances shop management systems even allow shop managers to identify scenarios in which the shop does not have either the relevant skills or equipment needed to fix a particular issue. You want to simplify decisions and accelerate processes. Most of all, you want to avoid wasting time on a part, procedure or solution only to find you don’t have what you need to address it.
Using Technology for Truck Driver Training
There is no doubt that bad driving raises the risk for a crash. Human error is the most commonly cited reason for heavy truck accidents. Whether it be driving the vehicle too fast, accelerating too harshly, or executing unsafe lane changes, risky driving behavior carries with it the risk of serious repercussions for your fleet.
Not as consequential, but equally costly, is how much bad driving creates more maintenance costs. Expect a lot more wear-and-tear on your equipment if your truck drivers are driving them in a risky fashion. Even seemingly minor infractions result in more costs. Studies show that traveling at 75 mph instead of 65 mph decreases fuel efficiency by 27%. For every mile per hour your truck drivers drive over 65 mph, there is a .14 mpg decrease.
Proper truck driver training goes beyond truck drivers. If your company is involved in passenger transport, the individuals operating your vehicles need to know how to interact with the public. No one wants to get on a shuttle and find a surly driver with a bad attitude. Even more, one of the best ways to change poor driving habits is to address the behaviors that underly them.
Your truck drivers deserve ongoing, relevant training to account for the needs of a changing marketplace. The entire point of ongoing training is to reduce risk, both to your truck drivers and to the fleet. Driving behavior also has an indirect impact on your insurance premiums. There is no part of your business safe from risky driving.
Many technological coaching and training solutions rely on the psychology behind learning. In order to optimize how a truck driver learns, you need to find out what works from a psychological and behavioral perspective. Learning represents the process of acquiring new information, knowledge, behavior or skill. Address underlying risky driving behaviors by teaching to the behavior.
Technological training solutions include apps, web interface portals, and desktop training solutions. Training apps can monitor results in real time, especially when they are integrated with a hi-tech ELD solution. There are also systems that can create real-time leaderboards for truck drivers. There is nothing wrong with a little friendly competition.
Truck drivers want to see progress more than anything. If you are evaluating them on their performance, you should be able to show them how they perform on an ongoing basis. Again, you never want to fear a competitive spirit. Especially if your truck drivers spend a lot of time out on the road. Anything you can do to make the driving team feel more like a family will work wonders for overall performance.
Technological training systems have many integrations, whether it be warnings or notifications on how the truck driver operates. In some cases, that information is transmitted back to the home office the moment it happens. Tracking on-road events is critical for any fleet manager and being able to do so in real-time allows for on-the-spot decision-making.
from Quick Transport Solutions Trucking Blog https://ift.tt/35cjo3T


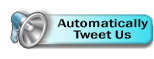
Sourced by Quik DMV - CADMV fleet registration services. Renew your registration online in only 10 minutes. No DMV visits, no lines, no phone mazes, and no appointments needed. Visit Quik, Click, Pay & Print your registration from home or any local print shop.
Thanks for sharing nice information with us. i like your post and all you share with us is uptodate and quite informative, i would like to bookmark the page so i can come here again to read you, as you have done a wonderful job. Ultrasound specialist
ReplyDelete