Want to get the most out of your fleet and maximize your bottom line? Remember, your vehicles are your money. You want to minimize downtime and ensure as much availability and on-road time as possible. But how do you do that? Well, you’ve got to make sure you stay on top of servicing, inspections, and repairs. But if you aren’t running an effective preventative maintenance program, none of that matters.
When you don’t have a preventative maintenance plan in place, you operate in a reactive mode. Instead of proactively preventing major breakdowns or equipment problems, you are merely responding them as they come, which results in more downtime then you otherwise might need to deal with. A PM program helps you prevent this.
If you don’t follow your vehicles’ maintenance schedule, the manufacturer might void your warranty entirely or at least in part. If a dealer or OEM can prove that it was through your own negligence that the problem occurred, you may miss out on needed upgrades or repairs.
Another Way to Look at It
Think of preventative maintenance as a regular health check up you might see at your doctor’s office. Your fleet is just the same. What if you feel fine on the outside, but more is going on inside? There are always some issues that may arise after-the-fact. And with these issues, if you do not address them immediately, they will only get worse.
One survey showed that average per vehicle downtime costs can range anywhere from $448 to $760 per day. These are not small numbers. If you have an issue with a vehicle that goes unrepaired, you lose money and productivity. And not only that, the high cost of parts and repairs can be crippling, never mind the loss of business you face. And if your reputation is hit? Expect to lose even more business.
Fortunately, you aren’t up the creek without a paddle. There are some quick basics you can cover to give yourself a better chance at catching minor issues until they turn into major problems. Because major problems turn into major headaches and can negatively impact your business.
But even more than that, you’ve got your vehicles to consider. They are, after all, your most important asset. You rely on these investments to keep your business rolling. So, while it may be tempting to skip important milestones that your vehicles need to effectively stay on the road, putting their longevity at risk just isn’t practical. Not keeping a regular eye on the individual components of your vehicles can significantly shorten their lifespan and create inefficiencies.
Let’s just rattle off a few of the major problems you might face if you are not catching them while they are minor:
- Greater fuel inefficiency
- Quick wear on tires
- Possible engine problems due to low oil
- Wiper blade issues
- Washer problems
- Radiator failure
- Flat batteries
Honestly, we could go on and on. The list of problems that arise when you aren’t catching problems early are multitude. But as long as you regularly monitor fleet maintenance, you won’t have to worry about these pesky problems.
Keeping Your Truck Drivers in Mind
Okay, we digress. We just said that your trucks are the most important asset in your fleet. We were wrong. Your most important assets are your truck drivers. And, the fact is, in the most serious of cases, mechanical failure can put the lives of your drivers and other road users at risk. Let us also remember that the regulatory agency governing us all expects trucking companies to prioritize safety.
The FMCSA clearly outlines how it believes how fleets should handle this situation. Under its regulations, drivers of commercial motor vehicles are required to inspect the basic components of a vehicle, including brakes, tires, lights, etc, and are built on the sound premise of ensuring a vehicle is safe to drive. In 2016, vehicle factors, most commonly tires, were recorded for 5.1 percent of large trucks involved in fatal crashes and 3.0 percent of passenger vehicles involved in fatal crashes, according to USDOT FMCSA data.
Regular vehicle inspections not only protect the lives of drivers, passengers and pedestrians, but also the livelihood of the fleet operator’s business. Preventative maintenance gives businesses peace of mind that their vehicles are safe to operate. The last thing they want is to find their equipment presenting a safety issue.
It also minimizes the risk of DOT violations, which can lead to fines, warnings, suspension or revocation of your ability to operate as a business, and even jail time. Many such violations have resulted in companies going out of business. The last thing you want is for yours to be one of them.
Truck drivers put a high value on maintenance because unforeseen downtime impacts their productivity and, in many cases, their income. A preventative maintenance creates a safe working environment and tells truck drivers that the fleet believes their safety matters.
Always Be Organized
If there is one thing that can quickly ruin an efficient operation it is a lack of organization. There is a lot to do and there are likely more than a few trucks cycling through the shop. Do you have important data on each truck already put together? You should know model, year, and mileage the moment you need to know it.
Do you have a specific process outlined for how your shop’s preventative maintenance should proceed? There are a lot of people involved in the workings of a healthy fleet and ensuring you have processes outlined avoids confusion. Here are some appropriate questions to ask as you evaluate your program:
- Who handles daily inspections?
- At what intervals are inspections handled?
- When defects or problems are found, who reports that information?
- Are the parts that may be needed in the shop or do they need to be ordered from a vendor?
- If you do need to order delivery parts, how long will they take to reach the shop?
The overall point is that you need to have the big picture in mind when it comes to your preventative maintenance program. That way you can properly determine interval levels and set up maintenance reminders. Maintenance reminders will ensure you don’t forget critical tasks.
Communication and Documentation are Key
One of the primary tenets of staying organized includes insuring everything within your shop is properly documented. You want to make sure you have easy access to vehicle data. This is especially important should an FMCSA audit ever arise.
Should you need to make a warranty claim, having proofs of service and related receipts to hand can make getting warranty repairs easier, especially in cases where dealers try to claim that maintenance wasn’t performed. You want to have all of this information stored together.
While it is incredibly important to ensure everything is properly documented, you also need to know who does what. What role does each person play, from the fleet manager to truck driver and shop technician? How are assignments and tasks communicated? Are you using a workflow management system to keep personnel and parts organized? Why not create some awareness posters and put them in your rigs and yard?
Make sure you properly set expectations to set yourself up for success and then measure the results. Analyze the results to see what’s working well and what isn’t. Monitor vehicle downtime, the total cost of repairs and the cost of avoidable repairs at regular intervals. This will help you see how well your preventative maintenance process is working and give you the opportunity to adjust if needed.
Harness Technology
Once again, we come back to the power of technology, but in this case, we want to draw your attention to a more little-known segment: trucking workflows. Fleet management systems go a long way to helping fleet managers and shop technicians keep track of parts. In many cases, add-ons to these programs can include usage-based alert triggers and workflows.
It is not uncommon for paperwork to be misplaced or damaged. Locating paperwork during an audit can be a chaotic process if you are not organized. And the last thing you want is for a DOT auditor to see you scrambling because the shop is a mess.
By using workflow management systems, databases, web-based portals, and more, you ensure you don’t lose documentation, time, or money. Your preventative maintenance program is the backbone of your fleet’s health. Have you taken a comprehensive look at yours?
from Quick Transport Solutions Trucking Blog https://ift.tt/2T4Ylvp


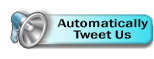
Sourced by Quik DMV - CADMV fleet registration services. Renew your registration online in only 10 minutes. No DMV visits, no lines, no phone mazes, and no appointments needed. Visit Quik, Click, Pay & Print your registration from home or any local print shop.
0 comments:
Post a Comment