The transportation industry is fresh off its highest peak in more than 10 years. As great as that may sound, it uncovered a difficult capacity problem. When bumping into the upper limits of what carriers can handle, the easy thing to do is throw more money at the problem.
However, when the market comes back to earth, carriers will be stuck holding the bill for surplus resources and find themselves facing the new challenge of cutting costs. Fortunately, there is a better way forward.
What Does the Data Say?
Data shows significant inefficiencies in the way carriers do business. Studies conducted over and over for the last two decades tell us detention plays a major part across a variety of critical industry issues. Combating detention by understanding its impact on driver safety and retention, working with shippers and drivers to remedy the problem, and looking to smarter detention management solutions to alleviate bottlenecks can lead to a win-win-win for all involved.
It’s simple economics. As demand rises and supply dries up, the market discovers a new equilibrium. Looking at freight volume in the United States after the Great Recession bottomed out in 2009, a regular pattern emerges where volume rises every year, only to fall as the calendar turns over.
Logistically, this sort of predictability is fantastic. Motor carriers can prepare for both the high and low tides. However, there has been a remarkable deviation in this pattern since the latter part of 2017. The market never let up. Instead of the usual dip, freight volume peaked in June 2018 to its highest point since 2007.
In all, the Cass Freight Shipments Index indicates a 30 percent swing in volume over a 16-month period ending in June 2018. Predictably, carriers hit capacity and rates took off: the Cass Freight Expenditure Index rose 31 percent over the corresponding period as a result.
As demand bumps up against trucking company capacity, shippers turn to the spot market to address their needs, which also has the effect of significantly increasing rates. The spot market is very near-term. A short run of events can increase spot rates 20 percent to 30 percent above contracted rates on any given day.
How Volatility Hurts the Bottom Line
High levels of volatility can really hurt shippers’ bottom lines. It takes a long time for asset-based carriers to see significant gains as operating ratios (OR) drop. Looking at OR over the last year, they dropped into the mid-80s — the lower the better, which is almost unheard of.
Railroads can operate down in the 50s and 60s because of the more consistent operating structure. Carriers do not have this amount of consistency. Anytime the market begins to surge, carriers can’t always take significant advantage of it right away. Detention rates don’t usually increase on the same level as carrier rates, especially on the spot market. And if they aren’t careful, trucking companies can lose a lot of money.
Take the Los Angeles market as one example. It was one of the hottest markets last year due in no small part to the impact of tariffs. There were a lot of inbound containers coming from China. Everyone was trying to get inventory into U.S. warehouses before they were charged an extra 20 percent to 30 percent just to get it there.
The Los Angeles market is already quite congested, averaging about 12 percent less utilization (in terms of hours of service) than the rest of the country. Every bit of that 12 percent equates to money lost. With an influx of freight moving in, fleets can’t scale up fast enough to manage these surges. The systems in place are designed to manage an average level of volume based on year-over-year trends.
With the convergence of factors that lead to a volatile market, utilization must be maximized. In 2018 the average load paid $2.03 per mile at its peak, not accounting for fuel. The average length of haul was approximately 550 miles, or about one day of transit.
Data indicated an average of 3.73 loads per truck per week. The remaining 1.27 more loads per week possible then amounts to $1,417 left on the table per week. A mere 10 percent increase in utilization at this rate would amount to another $141 per truck, per week. These are big differences.
What’s the Takeaway?
The takeaway: the market is inefficient. It’s already saturated with motor carriers, and even if capacity were expanded, a predictable cooling phase is likely to come reversing all growth measures. The extra capacity leads to excess cost, rates sink, and the industry then needs to retract.
Trucking companies now have the leverage to go back to these shippers that got dinged in late 2017, 2018, and say listen, the market was super-hot, but it has cooled off now, and we don’t want to get into a situation where it’s back and forth. A long-term management strategy including things like detention can really make a big difference to the bottom line.
A “good day” for a driver included 7.3 hours on the road on average out of a possible 11 hours of available drive time. After the HOS changes, “good” days shrunk to only 6.5 of a possible 14 hours on the road. That’s more potential drive time, yet less actual. Needless to say, there are significant hours being left on the loading deck.
It’s often left up to carriers to solve the detention issue. The problem is that when you leave it up to the carrier, it conflicts with the Golden Rule of Customer Service: ‘The customer is always right.’ Can a motor carrier realistically tell a customer he or she is wrong when the carrier wants to maintain its hold on a lane or freight contract?
Detention permeates to every single item on the American Transportation Research Institute’s (ATRI) annual list of “Critical Issues in the Trucking Industry.” By having a frank conversation between carrier and customer, each issue of the day — from driver retention to infrastructure to truck parking — could be positively effected through the lens of addressing detention.
While potential changes are on the horizon for HOS rules and sleeper berth flexibility, no one can predict if or when that may happen. The adverse effects of the government shutdown or the realigned Congress may delay the passing of rules relief or budget for infrastructure improvements. Addressing manageable inefficiencies in detention is the most tangible a path toward a solution right now.
What do Truck Drivers?
What are the key factors that make “customers of choice” for trucking companies? These shippers are mindful of safety, in-and-out time, overnight parking, appointment flexibility, amenities, and employ pleasant personnel — a list that echoes many of the same critical issues mentioned in the annual ATRI study.
In one of the most famous scenes in the first Jurassic Park film, everything starts to go wrong for the main characters at the T-Rex exhibit. There, a chained goat awaits consumption, yet when the mighty T-Rex shows up, our heroes wonder why it doesn’t feed on the restrained animal. One of the characters reasons that the T-Rex probably doesn’t want to be fed; it wants to hunt.
Could it be that drivers are much like that? They want to be running miles, to be productive. They don’t want to be fed the smaller amounts of money for sitting and being detained. A lot become angry that they are being paid for detention. They just want to get out of that situation, get moving, and start being productive.
For this reason alone, motor carriers need to have that one-on-one relationship with their truck drivers with open conversations. Otherwise, stress will build, which leads to accidents and turnover.
Things to Keep in Mind
Trucking companies need to keep their lines of communication open for immediate and timely reporting of any issue and should for any driver in the fleet. Once an issue reported, operations and safety people must work to define the issue and follow up with the driver by phone to clearly understand what’s happening. Once the problem is clearly identified, it should be assigned to leaders for follow-up. Follow-up with the driver is maybe the most important piece.
It may start with a simple phone call. The company should maintain a portal where all existing issues and outcomes can be viewed by any driver. A common issue includes getting facilities included on locations where drivers are detained. Another is navigating the problem of having to leave shipping locations when drivers are out of hours due to the six hours rule — in which case the fleet advises its drivers to call in to ensure there are no incidents.
Considering the “super-hot” market of late, what are carriers in for next? Will the market continue to bump up against the capacity ceiling, struggling to meet demand and further exposing inefficiencies? Or is it standing at the edge of a precipice, the natural fallout after any such ascent? Only time will tell!
from Quick Transport Solutions Trucking Blog https://ift.tt/2ZYwPny


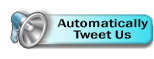
Sourced by Quik DMV - CADMV fleet registration services. Renew your registration online in only 10 minutes. No DMV visits, no lines, no phone mazes, and no appointments needed. Visit Quik, Click, Pay & Print your registration from home or any local print shop.
No comments:
Post a Comment