Do you have an effective tire program? Your tractor tires are the workhorses of your company. They provide the rolling power to get your loads from point A to point B. This is what makes tire matching so important. Matching the tires to your application is critical for both safety and efficiency reasons. Once that is done, your most basic considerations should be traction, tread life and rolling resistance.
It really is all about tire selection. You must know how your trucks workday in and day, then narrow down your choice of tires to meet as many of those operational criteria as possible. You may be running on-road and off-road applications. The environment is just as important as the tread the vehicle is riding on.
There are many things to evaluate when considering a tire’s overall performance arc. Consider the following as you set up a comprehensive tire program. Tires must:
- Suit the nature of its operations
- Fit to its truck drivers and their habits
- Match driving locations
- Be compatible with maintenance practices
- Fit your budget
- Keep fuel costs low
Whether you are looking at the best cost per mile or best cost of ownership, considering the prior factors will help you decide. The fact is all trucking companies want to lower their operation costs. One of the best ways to do this is through your tire program. By adjusting to the needs of the business, you can find the right balance between toughness, long life, and lower fuel consumption.
How to Find the Right Tires
Don’t feel cornered into making a big tire purchase based on price alone. Cheap tires are cheap for a reason. You will often find that you sacrifice quality for quantity, you are also sacrificing safety along with it. Cheap tires blow more often. The last thing you want is one of them blowing while your rig is out there on the road. Take advantage of the tools companies have to offer.
We have talked a lot about big data, and it is very likely you have data at your disposal, especially if you use telematics systems. Are you taking advantage of your data? Many ttire maintenance software and tire pressure monitoring apps can assist you. As they monitor tire installations, you can assess in real-time the performance of tires in the field or on the road. You can easily diagnose problems before they turn into accidents.
Trucking companies of all sizes work with local dealers. Do you work with yours when you acquire tires or set a strategy? Do not hesitate to work directly with your local tire dealer. They have the skills and tools necessary to help you determine which tire is most appropriate for your application, needs, and vehicles.
Finally, have you tapped into the wellspring of knowledge put together by the American Trucking Associations’ Technology & Maintenance Council (TMC)? They have a ton of excellent resources for those who need more information about what tires to choose. Fleet technicians can use TMC Recommended Practices to identify test procedures to ensure the right tire is acquired.
A Look at Wide-Base Single Tires
Have you ever considered wide-base single tires? It may be that you think conventional duals work just fine for your application, but wide-base options might be worth a second look. Why? Because weight savings remains the primary benefit of using wide-base truck tires.
When combined with an aluminum rim, wide-base tires can save up to 1,100 pounds. Of course, the market has seen an increase efficient dual combinations, but saving fuel is not the only benefit of wide-base tires. They also make the technician’s job far easier and play a role in preventing the types of catastrophic damage associated with a blowout.
Still, wide-base tires do not come without their own unique considerations. Some trucking companies report more irregular wear and shoulder wear. As a result, some trucking companies mix their options by utilizing narrow- or mid-track axles. This way they can convert back to a dual configuration if running wide-base tires doesn’t pan out.
That also requires the use of offset wheels, which have been linked to increased inside shoulder wear on the tires. These problems arise when there is excessive axle flexing. As the axles flex, a negative camber condition forms at the wheel.
You can mitigate this irregular wear after moving to wide-track axles with zero-offset wheels. But this can cause problems in the event of a failure or at the end of the vehicle’s service life, since if you wanted to put duals back on the axle, you’d be more than 102 inches wide.
Proper inflation and maintenance are critical no matter what tires you use, but even more so with wide-base tires. You have a lot riding on one tire when you operate in a wide-base configuration. Make sure you are balancing your tires and checking your vehicles alignment on a regular basis. When conducting preventative maintenance, you may also want to do a bearing end-play check on every wheel. It may take more time than normal, but it is necessary.
Keeping Inflation in Mind
Inflation pressure should be top of mind for your shop. This is a matter of safety, fuel efficiency, tire life, tread wear, and bottom line. Fortunately, there are comprehensive systems on the market to help fleets manage tire inflation in real-time. Whether you already use a fleet management system with them integrated in or use them separately, tire pressure monitoring and inflation systems should be in place across the fleet.
Tire pressure monitoring systems have come a long way in a short period. The systems used to be nothing more than a light on the dash blinking on and off if there was a problem. Today’s modern TPMS systems are leaps and bounds above their predecessors. Rigs can now link up their tire pressure systems with other telematics systems and databases at play within the fleet.
Gone are the days when you couldn’t put datapoints together without great effort. Now fleets can upload comprehensive tire performance profiles and upload failure information into the fleet systems and on their dashboards. Connect these systems together to provide exceptions and update maintenance logs on the fly. Telematic links to some systems mean reams of data can be streamed from the tires back to fleet headquarters.
Also consider automatic tire inflation systems. It wasn’t long ago that these systems were only available on trailers. Today, you can find variations for use in drive axles, though they are not widely used across the country. Trailer tire inflation systems have been in use for a long time, however. And there are many OEMs to choose from. But how do they work?
Automatic tire inflation systems work by relieving more stress on the tires. There are no moving parts to speak of, a bare minimum electrical components, and there are few modifications required to the equipment on hand. Neither do they require complex assembly. They can be installed on the assembly line or retrofitted just as easily.
Modern-day systems should provide TPMS and ATIS-integrated telematic capabilities. Fleet managers should have access to specific alerts provided when the system activates. The best part of these combo systems is that they take a truck driver mistake out of the equation. Everyone benefits in such a scenario.
The Industry is Changing
Sure, we are at an inflection point in trucking technology. As good as current offerings are, new technology will soon transform tire maintenance services in ways we can’t imagine. As motor carriers become more complex, the need for accurate, real-time, actionable tire data will only. OEMs and the trucking companies who rely on them will need to innovate.
Unfortunately, we still live in a day when most tire technicians measure metrics such as inflation and tread depth levels with a manual gauge, jot down the results on a piece of paper, and then manually enter that data into the system. This entire process takes far too much time. Many fleets have turned to outsourcing tire maintenance programs, but there is value to managing them in-house.
Now the tire companies can supply the fleet technicians with special tools to take tire measurements. The information obtained can be uploaded into the fleet management system using a cellular, Bluetooth or Wi-Fi connection. Web portals can be maintained so that technicians, truck drivers, and fleet managers can view necessary tire information.
What does this mean for trucking companies? Even small fleets will have access to information critical to helping them maintain their tires well. All shop technicians and fleet managers should remember that maintaining a proper tire program is about safety, fuel efficiency, and a health bottom line.
With this level of real-time transparency in play, soon even small truck fleets will be able to see vital tire operational information right away, enabling them to immediately adjust their tire management programs if necessary. Taken as a whole, these capabilities can help fleets make end-runs around manpower and time issues whiles improving uptime and tire asset utilization — all of which ultimately reduces fleet operating costs.
from Quick Transport Solutions Trucking Blog https://ift.tt/32Slu8j


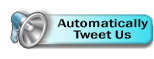
Sourced by Quik DMV - CADMV fleet registration services. Renew your registration online in only 10 minutes. No DMV visits, no lines, no phone mazes, and no appointments needed. Visit Quik, Click, Pay & Print your registration from home or any local print shop.
0 comments:
Post a Comment