As long as heavy-duty trucks encounter water or road deicers, rustjacking will continue to wreak havoc on brakes. Technicians need to know how to spot rustjacking as well as know what to do if it’s found.
Rustjacking on brakes is not only dangerous, but it can get a truck owner’s vehicle pulled out of service. Combating rustjacking is a team sport, involving truck owners, technicians and brake vendors.
Rustjacking is most identified by a layer of rust between the drum brake shoe table and the friction. A technician will be able to see the friction is delaminated — separating into layers — or may see cracking along the edge of the friction lengthwise, says Mark Holley, director of marketing and customer solutions, wheel-end, Bendix Commercial Vehicle Systems.
Because the friction material is riveted to the shoe table, the rust will grow and push the friction away from the shoe table until the friction material cracks.
“Sometimes you will see measurable gaps if you inspect the sides of the shoe between the table and friction before cracking starts. It is very often hard to see the rust while inspecting the side of the brake shoe. When you de-line the friction from the table, you will clearly be able to see if rust was the issue as you often will see 1/16 to 1/8 of an inch or more of rust formed on the table,” says Scott Myers, director of marketing and engineering, Marathon Brake Systems.
Causes of rustjacking
Rustjacking can be caused by “harsh” anti-icing liquids in winter road solvents on roads, combined with moisture that penetrates the brake shoe coating while equipment is at rest, says Eric Coffman, senior product manager, Meritor aftermarket.
“This causes rust to build up on the brake shoe table. As rust builds up, it pushes outward against the lining, ‘jacking’ it up between the rivets until the lining cracks. Rustjacking is more often found where intense brake heat cannot dry out the shoe table,” Coffman says.
Bendix Commercial Vehicle SystemsHolley adds as the rust builds up on the steel of the shoe, it pushes upward on the friction, causing cracks and breakage, which also allow additional space for water and corrosive materials to exacerbate the situation.
The main way rustjacking can be caused is by micro abrasions between the friction material and the shoe table, says Myers.
“Friction material is, of course, very abrasive, it is also porous on the inside diameter (ID) of the friction. During braking, especially in applications that often require a high pressure to be applied, the ID of the lining can ‘scrape’ the paint from the outside diameter of the brake shoe, exposing bare steel that can rust very quickly,” he says.
[Related: The Battle with rustjacking]
“Think of it this way: Even though the friction is securely attached by rivets to the brake shoe, with each repeated stop, the lining rubs against the brake shoe and moves just a bit back and forth,” Myers says. “This is the micro abrasion that can remove the coating and expose bare steel that will quickly rust.”
Myers adds rustjacking also can be caused a couple different ways that are less common and result from quality issues while shot blasting the steel or not following sound coating practices.
For example, if a brake shoe has not been properly cleaned before the coating process, there can be residue rust that will continue to grow after the shoe is coated that could cause rust to grow through the paint.
[Sidebar: Rustjacking and reman]
Another cause is “if the shoe coating is of an inferior specification, it could disappear quickly under chemicals or by being crushed under the pressure of braking, exposing bare steel on the shoe table where rust can form,” Myers says.
Other experts echo Coffman’s thoughts regarding brakes susceptible to rustjacking when parked.
“When you have vehicles parked for a long period of time, depending on where they’re parked, ice, moisture, sitting in the mud, are vehicle conditions that can accelerate rustjacking,” says Jay Pagano, industry veteran and brake systems expert for Global Parts Network, part of the VIPAR Heavy Duty Family of Companies.
Holley says, “Trailer brakes that sit idle for long periods are particularly susceptible to rustjacking, because moisture lingering beneath the brake material doesn’t get burned off during regular brake applications.”
The battle against rustjacking
There is only so much truck owners can do to prevent rustjacking. But regular maintenance, being mindful of where they park their trucks and buying quality brake shoes and friction can delay the process over time.
Myers suggests vehicle owners use a friction material that is very strong and conformable, also known as a friction’s toughness.
In addition, he says there are thin adhesive membranes that can be applied between the shoe table and friction during the riveting process that help mitigate the abrasion process that could expose bare steel on the shoe table. “There are a variety of tricks to combat the issue; the key is to never allow any exposed non-coated metal on the table under the friction blocks.”
Examples of rustjacking on brakes.MeritorThere also are special coatings that have been developed to apply to the shoe table. These coatings can resist the micro abrasions, so the coating does not get removed, he says.
For example, PlatinumShield III is Meritor’s solution for rustjacking.
“In developing PlatinumShield III, Meritor’s aftermarket engineering team discovered a refinement in the process that provides superior adhesion of the coating to the surface of the shoe. Superior adhesion enables the coating to protect the brake shoe, increasing the shoe’s ability to withstand the corrosion caused by salt,” Coffman says.
Likewise, Bendix offers its PermaGuard coating for new aftermarket or remanufactured shoes. Bendix says it’s a highly engineered protective layer of paint applied to the shoe, and the coating helps virtually eliminate rustjacking.
“The effects of rustjacking aren’t caused solely by the quality of a brake shoe’s coating. The right friction is an often-overlooked factor. Lower-cost friction materials tend to be manufactured from shorter fibers and have a lower flexural strength, which makes them more prone to delamination or deformation under the pressure caused by rustjacking,” Holley says.
Once rustjacking is detected, Myers says the brake shoe cannot be repaired and must be replaced. “Rust keeps propagating rapidly once it starts. The cores can be sent back to be relined, and the shoe (core) can go back into service later after it undergoes the reline process, but the friction is not repairable,” he says. [See sidebar above: “Rustjacking and reman”]
from Overdrive https://ift.tt/3iWkbyo


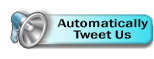
Sourced by Quik DMV - CADMV fleet registration services. Renew your registration online in only 10 minutes. No DMV visits, no lines, no phone mazes, and no appointments needed. Visit Quik, Click, Pay & Print your registration from home or any local print shop.
0 comments:
Post a Comment